- QMS
- MES
- DX
製造業におけるデジタルトランスフォーメーション:連携したQMSとMESによるサイロの打破
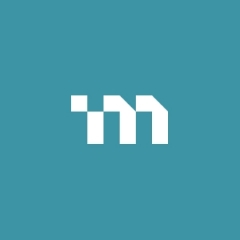
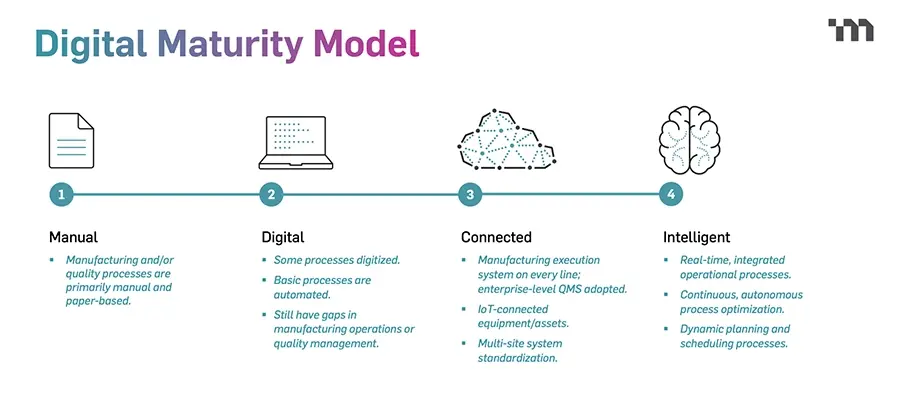
本記事はマスターコントロール本社公式ブログの日本語版です。
現代のデジタル時代において、企業は運営に先進技術を統合する方法を継続的に模索しています。特に製造業はエコシステムの連携によるデジタルトランスフォーメーションから大きな恩恵を受けることができます。この記事では、真に連携された製造環境を実現するために、品質管理システム(QMS)と製造実行システム(MES)ソフトウェアを統合することの重要性について探ります。
連携した品質・製造エコシステムの構築
マスターコントロールが主催したウェビナーなど、業界全体での最近の議論は、製造業におけるデジタル成熟度への道のりに光を当てています。主な目的は、サイロを打破し、より統合された効率的な製造エコシステムを育成することです。
マスターコントロールのニコール・シャーマン、ケイトリン・ミントン=スミス、ジェシカ・マドセンは、デジタル的に成熟した連携製造環境に向けての洞察を共有しました。ウェビナーの主な焦点は、先進技術を活用して分断されたシステムを接続し、生産情報のシームレスな流れを実現することで、製造業におけるデジタル格差を埋めることでした。
デジタル格差の理解
デジタル技術が私たちの日常に不可欠な世界に生きていますが、特にライフサイエンス分野の製造業者は新技術の採用において遅れをとることが多いです。多くのプロセスは依然として紙ベースであり、デジタル化によって避けられるはずのエラーが発生しやすい状態です。マッキンゼーの報告によれば、ライフサイエンス企業はデータリソースの不足やデジタルトランスフォーメーションに対応できない全体的な企業文化により、デジタル成熟度において他の産業に遅れをとっています。
しかし、医薬品の研究開発など、技術が完全に受け入れられている分野もあります。人工知能(AI)が創薬に使用されたり、患者データの予測を組み込んだ医療機器、個別化された薬剤生産などが進んでいます。こうした進歩にもかかわらず、紙での作業に慣れている品質部門や製造部門はデジタルトランスフォーメーションで遅れをとっていることが多いです。
デジタル成熟度に関する研究洞察
デジタル格差を理解するため、マスターコントロールは製薬、医療技術、バイオテック、バイオロジクスなどのライフサイエンス分野で300人以上の品質・製造専門家を対象に広範な調査を実施しました。この調査によると、回答者の50%がデジタル化を高い優先事項と考え、正式な計画を持っているものの、大多数はまだ「デジタル」カテゴリーに分類され、完全な接続性を欠いたデジタル成熟度の中間段階にあることが明らかになりました。
デジタル成熟度モデル
企業が現在の段階と将来の目標を特定するのを支援するため、デジタル成熟度モデルが開発されました。デジタル成熟度の4段階は以下の通りです:
- マニュアル:主に紙ベースと手動プロセス。
- デジタル:一部のプロセスがデジタル化され、基本的な自動化がある。
- 連携:全システムとソフトウェアの深い統合により、包括的なデータ分析が可能。
- インテリジェント:最小限の人間の関与でAIなどの先進技術を活用し、自律的なデータ交換が最適化されている。
回答者の半数以上がデジタル成熟度の次のレベルへの進化を望んでおり、完全なデジタル統合に向けた集団的野心が浮き彫りになりました。
連携エコシステムのパワー
連携された製造・品質システムのエコシステムは、大幅に優れた成果をもたらします。利点には以下が含まれます:
- 可視性の向上:部門間でのデータ共有とリアルタイムの可視性により、より速く、より良い意思決定が可能になる。
- 効率的なワークフロー:自動化により手動エラーが減少し、プロセスを接続・加速させることで、生産サイクルと品質チェックが迅速化する。
- コスト削減:品質イベントの減少と管理の容易さ、手動エラーの減少、無駄の削減により、大幅なコスト削減につながる。
マスターコントロールのアプローチ
マスターコントロールは単一の統合プラットフォーム上で品質と製造を組み合わせています。MasterControl Manufacturing Excellenceソリューションは、品質管理システムだけでなく、ERP(企業資源計画)やLIMS(実験情報管理システム)などのサードパーティシステムとシームレスに統合し、データの流れと運用の透明性を確保します。このソリューションの分析エンジンはさらに、さまざまなソースからのデータを統合することで、堅牢なデータ駆動型の意思決定を可能にします。
実世界のシナリオ
組織の標準作業手順書(SOP)の更新を例に考えてみましょう。連携したシステムでは、更新されたSOPが生産プロセスに直接統合され、オペレーターが常に最新情報を持つことを確実にし、コストのかかるミスややり直しを避けることができます。別のシナリオは、生産中の逸脱の管理です。連携システムは逸脱が発生すると品質管理担当者に自動的に通知し、即時対応を可能にして遅延を防ぎます。
小さく始める
連携エコシステムへの移行は圧倒的に思えるかもしれませんが、そうである必要はありません。企業はログブックのデジタル化など、小さなプロセスからデジタル化を始め、徐々により包括的なシステムへと拡大できます。将来の拡張性と全業務にわたる接続性を確保するために、堅牢な統合戦略を提供するプロバイダーを選択することが重要です。
結論
連携エコシステムを通じて製造業におけるデジタルトランスフォーメーションを受け入れることで、継続的改善の取り組みを強化し、運用効率とコスト削減の向上につながります。小さく始め、段階的な実装に焦点を当てることで、初期の障壁を克服し、デジタル製造の可能性を最大限に活用する道を歩み始めることができます。
より詳細な洞察やデジタル成熟度を達成するためのステップバイステップのガイドについては、マスターコントロールの製造業におけるデジタルトランスフォーメーションに関するエグゼクティブレポートを参照してください。このリソースは、最適な結果を得るために品質と製造プロセスを整合させ接続する方法を概説しています。
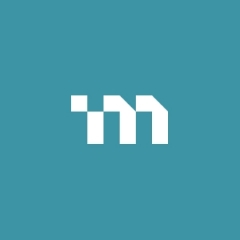