- QMS
- MES
- 食品・飲料
過去10年間で、ウェリントンフーズ社のサービスに対する需要は大幅に増加しました。この消費財メーカーは、紙ベースのシステムでエラーが発生しやすく、市場投入までの時間が長くなり、事業規模を拡大するには煩雑すぎるという問題を抱えていました。
「紙ベースの包括的なシステムもありましたが、会社が成長するにつれ、紙ベースのシステム管理が難しくなっていきました。プロセスの改善・管理を実証する方法を検討する中、テクノロジーで解決できる方法が数多くあることを突き止めたのです」と、ウェリントンフーズ社の社長、トニー・ハーナック氏は述べています。
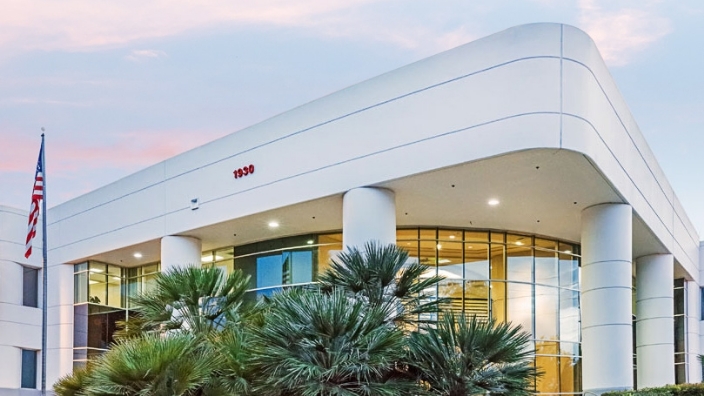
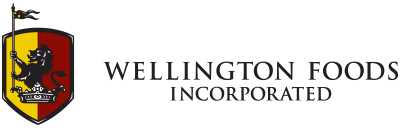
- フォーカス
- 液体および粉末状の栄養補助食品の受託製造業者
- 本社
- カリフォルニア州コロナ
- 従業員数
- 150人以上
- 課題
-
紙の作業を排除して、生産拡大を実現し、遅延の原因となるデータ入力ミスとプロセスの非効率性を減らし、経営陣と顧客の可視性を向上させます。
- ソリューション
-
Quality Manufacturing - 成果
-
マスターコントロールのソリューションを導入することで、ウェリントンフーズ社は需要への対応力を高め、時間がかかっていた生産後のレビュープロセスを72時間まで削減し、可視性を高め、市場投入までの時間を短縮しました。
クラウドベースのソリューションは拡張性が高く、ドキュメントエラー、市場投入までの時間、コンプライアンスの容易さなど、多くの問題点を解決する洗練されたツールを利用できる一方で、コストのかかるインフラに投資する必要がないことから、同社はマスターコントロールを選びました。
ウェリントンフーズ社は、米国食品医薬品局(FDA)、カリフォルニア州、および顧客の規制を受けています。コンプライアンス維持の一環として、組織は栄養補助食品業界に対するFDAのCFR Part 111規制の中心であるプロセス管理を実証する必要があります。
これらの取り組みを合理化するために、ウェリントンフーズ社は、マスターコントロールの特許取得済み(米国特許第10,324,830号)のValidation Excellence Tool (VxT)TMを採用しました。これは、ソフトウェアのバリデーションにかかる時間と労力を劇的に削減する、世界初のリスク評価アプリケーションです。
「マスターコントロールのような自動化されたソリューションにより、紙ベースのソリューションよりも多くの生産処理を管理できることが分かりました。」トニー・ハーナック氏 ウェリントンフーズ 社長
Right First Time(初回から適切)な生産、可視性、高い顧客満足度を実現
電子バッチ記録(EBR)へ切り替えることで、マスターテンプレートにデータ制限を組み込めるようになり、誤った入力は拒否されるかシステムオペレーターに警告されるため、一般的なデータ整合性に関する問題が解消されます。最新のトレーニングを受けていないオペレーターは、システムにデータを入力することができません。
このようにして、ミスはほぼ即座に回避・修正され、エラーを減らすことで、例外によるレビューを実施し、Right First Time(初回から適切)な生産を実現できます。
デジタル化することにより、生産プロセス全体をより把握できます。システム間が接続されていることで、単一のダッシュボードでリアルタイムに可視化され、管理者は変更に関する決定を下して効率を向上させることができます。紙ベースのシステムでは、このように俊敏に対応できません。
「当社の経営陣は従業員が本来するべき大切な業務に集中するためにマスターコントロールによるElectric BatchRecord(EBR)の電子化を採用しました。紙の処理作業ではなく本質的な業務に集中することによって、製品の品質をより向上させる事ができます。」ロビン・ジョイナー氏 ウェリントンフーズ マスターコントロールシステム管理者
また、可視性の向上により、製品が製造現場のどこにあるのか、いつ完成するのか、顧客の仕様や規制をどのように遵守しているのかなどの情報をリアルタイムで提供し、プロセスで品質が保証されていることを示すことができるため、顧客との信頼関係を確立し、維持できます。
「納品まで滞りなく進められる仕組みを確立することは、当社に任せられています。例えば、納期が6週間後のマルチビタミンの注文があった場合、膨大な数の製品を蓄積し、すべてを承認し、スケジュールを立て、すべてを一度に生産する必要があります」とハーナック氏は言います。
紙の削減とデータの整合性の向上
以前は、紙ベースのシステムが原因で発生したエラーにより、生産後のレビュープロセスが完了しなかったため、製品の出荷を待つ間に遅延が発生していました。マスターコントロールを導入することで、これらの分野については大幅な改善がみられました。製造現場でのデータ入力ミスは90-100%減少し、10-15日かかっていた生産後のレビュープロセスは、今では72時間で完了するようになりました。遅延が減ることで、従業員が重要なビジネスプロセスに集中できる時間が増え、結果的に市場投入までの時間が短縮され、貴重な競争力を得ることができます。